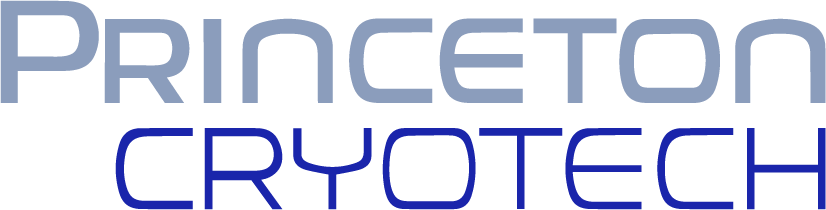
Princeton CryoTech is a leading national distributor for liquid nitrogen freezers and biomedical storage equipment.
Learn More About Our CompanyWe pride ourselves in our past 27 years of selling and servicing MVE, earning the trust of our customers since 1990.
We don’t consider ourselves freezer salespeople, we consider ourselves technicians and engineers who happen to sell cryogenic storage equipment. Where others are quick to sell and move on, Princeton CryoTech creates lasting relationships with clients who value ongoing service and support. Everything we sell automatically comes with lifetime technical support, and discounted preventative maintenance and service contracts.
Be careful who you reach out for assistance servicing your cryogenic freezer. Many companies claim knowledge in this field, but an uninformed service call can often leave your freezer worse off than it started. When someone quotes you an expensive repair, don’t hesitate to ask us for a second opinion. Sometimes a seemingly serious issue is actually a simple repair.
Ensuring that your liquid nitrogen storage freezer is working correctly and optimally is our top priority, and our customers are often surprised at how simple tweaks can dramatically increase lab efficiency. Taking from decades of hands on experience servicing and repairing freezers, there is little we have not encountered.
Our web store contains mountains of technical data on our MVE biomedical products, including spec sheets, catalog sheets, user manuals, as well as technical tips MVE has posted over the decades. (insert link to knowledge and resource page on princetoncryo.com here?)
If you are looking to purchase this equipment outright, our web store shows published list pricing, however we typically offer competitive discounts when quotes are requested.
Why not catch issues before they become a problem? Our services start with systems checks and recommendations, all the way up to full maintenance plans with parts’ replacement.
Our maintenance can include temperature and LN2 level calibrations, freezer log download and comprehensive history review, regulr parts replacement, and controller software upgrades.
At times, older freezers need to be fully thawed to repair certain nagging issues, such as ice buildup, temperature probe replacement, or level reading issues. Our thaw procedures include a full thaw, moisture purge, cleaning, and then the full systems and parts check, before restarting the freezer.
Not every facility has a spare freezer to move your samples to, so we have several spare freezers in stock available for rent to facilitate this procedure.
Please feel free contact us for a consultation or a quote for your facility’s freezer maintenance, we tailor our service for each customer’s unique needs .
Our proprietary 10-page document is specific to your freezer and performed at installation. A qualified technician sets up the freezer for operational and performance qualification, setting up the freezer controller to log every 10 minutes, providing 1-2 weeks of validation reporting to be included with the final documentation.
Contact our experienced team to get a custom quote for your specific IQ/OQ/PQ and validation needs.
Why not catch issues before they become a problem? Our services start with systems checks and recommendations, all the way up to full maintenance plans with parts’ replacement.
Our maintenance can include temperature and LN2 level calibrations, freezer log download and comprehensive history review, regulr parts replacement, and controller software upgrades.
At times, older freezers need to be fully thawed to repair certain nagging issues, such as ice buildup, temperature probe replacement, or level reading issues. Our thaw procedures include a full thaw, moisture purge, cleaning, and then the full systems and parts check, before restarting the freezer.
Not every facility has a spare freezer to move your samples to, so we have several spare freezers in stock available for rent to facilitate this procedure.
Please feel free contact us for a consultation or a quote for your facility’s freezer maintenance, we tailor our service for each customer’s unique needs .